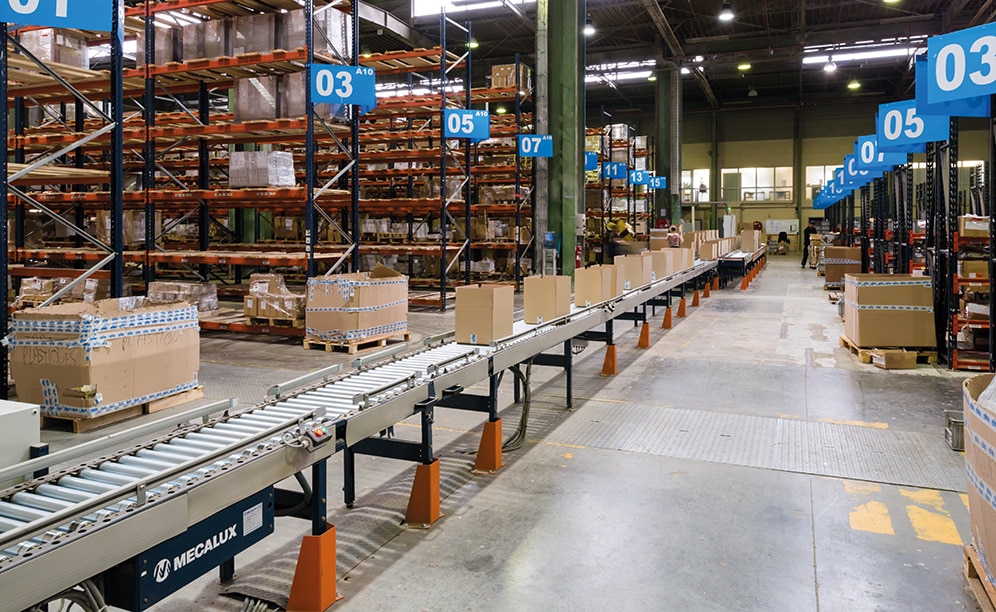
Un completo circuito de transportadores multiplica la productividad en el picking del fabricante francés de productos para el bricolaje Vynex
El centro de distribución de Vynex aumenta sus expediciones con un circuito de transportadores y estaciones de picking
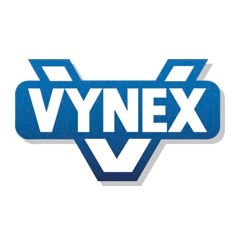
Mecalux ha suministrado un circuito de transportadores en el centro de distribución que Vynex posee en las Ardenas (Francia). Esta solución comunica todas las áreas que componen el almacén, agilizando y aumentando al máximo el rendimiento de la preparación de pedidos, operativa principal de esta instalación.
Quién es Vynex
Vynex es una marca francesa reconocida en el sector de la ferretería que se creó en 1920 en la región de las Ardenas.
En los años 50, la compañía anticipó la expansión que tendría el bricolaje en el público general y creó una gama específica para usuarios domésticos, mientras continuaba desarrollando su oferta para profesionales.
Esta visión impulsó su crecimiento y, en la actualidad, los productos de Vynex se comercializan en gran parte de Europa, con vistas a expandir su mercado a nuevos países del continente en un futuro.
Necesidades y solución
El centro de Vynex en las Ardenas, dedicado principalmente al picking, cuenta con más de 20.000 referencias de tamaños, pesos y clasificaciones distintas que se almacenan teniendo en cuenta sus características.
La compañía necesitaba que sus operarios pudiesen preparar muchos pedidos a la vez de la forma más eficiente posible, así como aumentar el número de expediciones diarias.
Tras analizar en detalle estos requisitos, Mecalux optó por suministrar un circuito de transportadores que discurre por el centro del almacén a una velocidad de 25 m/min y une todas las áreas. A lo largo del recorrido, hay cinco estaciones de preparación de pedidos.
Esta solución confiere gran agilidad a la hora de hacer picking, ya que los operarios no deben recorrer todo el almacén para seleccionar los productos que forman cada pedido, sino que tan solo trabajan en un área asignada.
El punto final del circuito culmina en la zona de expedición, donde los pedidos se clasifican por rutas o destinos antes de ser distribuidos.
Preparación de pedidos
El método de picking que se ha elegido en este almacén está basado en el criterio de hombre a producto, es decir, los operarios se desplazan hasta las estanterías utilizando carros para recoger manualmente las referencias que el software de gestión de almacenes (SGA) les señala. La preparación de los pedidos se realizará próximamente mediante un sistema por voz a fin de mejorar aún más la calidad del servicio.
Las tarimas de reserva se almacenan en racks selectivos ubicados en el inicio del circuito de transportadores. La reposición de la mercancía se realiza en las horas que hay un menor volumen de preparación. El proceso de preparación de pedidos se inicia con la conformación manual de cajas. El SGA indica el número y su tamaño, teniendo en cuenta la composición de cada ola de preparación. En el almacén de Vynex se emplean principalmente dos tipos de cajas: 570 x 370 x 235 mm y 400 x 285 x 235 mm, con un peso máximo de 25 kg.
Se han instalado cinco estaciones de picking, cuatro de ellas agrupadas –una enfrente de la otra–, separadas por el transportador principal que circula en el centro; y una simple, adosada a la pared. A cada una de ellas le corresponde un número determinado de estanterías (sector). Los operarios que pueden trabajar en cada estación varían dependiendo de la cantidad de pedidos que se deban preparar.
Las estaciones están formadas por rodillos no accionados por ningún motor, de modo que los operarios pueden desplazar las cajas manualmente hasta la posición más cómoda.
Cuando los trabajadores han terminado su parte del pedido, introducen las cajas en el transportador central que las traslada hasta la siguiente estación para que continúe el proceso. En el supuesto de haberse completado, se encaminan directamente hasta la zona de verificación y embalaje.
Allí se verifica el peso, se comprueba que el pedido esté finalizado y no haya errores. Por último, se cierran las cajas, se embalan, etiquetan y se emiten los albaranes y la documentación correspondiente.
En el área de expediciones, los pedidos se clasifican automáticamente en cinco canales ubicados delante de los muelles de carga. Los operarios distribuyen la mercancía en las distintas tarimas, clasificadas por clientes o rutas de envío.
En cada uno de los canales, se han instalado monitores que ofrecen a los operarios toda la información necesaria para clasificar correctamente los pedidos
Los transportadores se adaptan a las características y distribución del almacén. El circuito incorpora líneas rectas, curvas y, además, se han abierto tres pasos que facilitan el acceso del personal mediante transportadores abatibles. Una vez los operarios lo han cruzado, recuperan su posición para continuar trasladando la mercancía.
SGA y control unidos
El SGA se encarga de organizar toda la operativa del almacén de Vynex y está en comunicación permanente con el módulo de control Galileo de Mecalux. Este da las órdenes de movimiento al circuito de transportadores, dirige las cajas a las estaciones o áreas correspondientes y finalmente las clasifica en los canales.
Beneficios para Vynex
- Flexibilidad en la operativa: la sectorización del almacén ofrece flexibilidad a la hora de preparar pedidos, ya que cada célula está asignada a un número de estanterías y operarios, que varía en función de la demanda.
- Rápido sistema de preparación de pedidos:la incorporación del circuito de transportadores automático permite agilizar al máximo toda la operativa.
- Almacén integrado: el circuito de transportadores une las distintas zonas del almacén. Así, los operarios no deben recorrer toda la instalación a la hora de preparar los pedidos, logrando la máxima eficiencia.
Almacén sectorizado de Vynex en Francia | |
---|---|
Capacidad de almacenaje: | 6.334 tarimas |
Ubicaciones de picking: | 23.618 (6.334 para tarimas) |
Nº de pedidos al día: | 5.000 |
Longitud de los transportadores: | 284 m |
Velocidad de los transportadores: | 25 m/min |
Galería

Mecalux optó por suministrar un circuito de transportadores que discurre por el centro del almacén a una velocidad de 25 m/min y une todas las áreas
Consulte con un experto